
The reliability of a part or component of aircraft hardware is only as good as its inherent design (supported by adequate maintenance) allows it to be. In fact, over 90 percent of generic part types show either random distribution of failure or gradually increasing probability of failure with age (Edwards, 1994). Airline experience indicates that hardware items wear out, but statistical old-age wear-out in complex mechanical, electrical, and avionic components is not a dominant pattern of failure. The application of new materials will not cause undue maintenance difficulties or hardship for the airlines provided the aircraft designer is familiar with component experience. Generally, the maintenance task evaluates sources of structural deterioration including accidental damage, environmental deterioration, and fatigue damage susceptibility of the structure to each source of deterioration the consequences of structural deterioration to continuing airworthiness including effect on aircraft (e.g., loss of function and reduction of residual strength, multiple-site or multiple-element fatigue damage, the effect on aircraft flight or response characteristics caused by the interaction of structural damage or failure with systems or power plant items, or in-flight loss of structural items) and the applicability and effectiveness of various methods of detecting structural deterioration, taking into account inspection thresholds and repeat intervals.
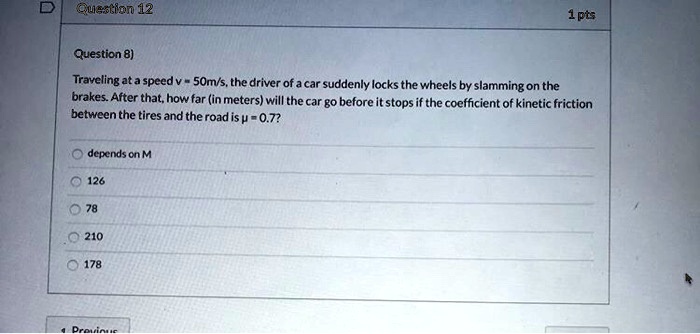
Any new aircraft program is based on assessing structural design information, fatigue and damage tolerance evaluations, service experience with similar aircraft structures, and pertinent test results.
